Introduction
Diesel generators play a crucial role in providing backup power during outages, emergencies, or in remote locations where grid power is unreliable. However, the performance and longevity of diesel generators are heavily dependent on the quality of the fuel they use. Poor fuel quality can lead to engine damage, decreased efficiency, and increased maintenance costs. Therefore, adhering to fuel quality standards is essential to ensure the optimal operation of diesel generators.
In this article, we will explore the importance of fuel quality standards for diesel generators, the potential consequences of using low-quality fuel, and the key parameters to consider when evaluating fuel quality. By understanding and implementing these standards, users can maximize the efficiency and reliability of their diesel generators.
Importance of Fuel Quality Standards
Fuel quality standards are a set of criteria and specifications that define the acceptable quality of fuel for use in various applications, including diesel generators. These standards are designed to ensure that the fuel meets certain performance, safety, and environmental requirements. 300kw diesel generator for oil and gas facilities to fuel quality standards is essential for several reasons:
1. Engine Performance: The quality of fuel directly impacts the performance of diesel generators. Low-quality fuel can lead to incomplete combustion, reduced power output, increased emissions, and overall decreased engine efficiency. By using fuel that meets the specified quality standards, users can optimize the performance of their diesel generators and ensure reliable power generation.
2. Engine Longevity: Poor-quality fuel can cause deposits to build up in the engine, leading to increased wear and tear, reduced engine life, and the need for more frequent maintenance. By using clean and high-quality fuel, users can extend the longevity of their diesel generators and reduce the risk of costly repairs or replacements.
3. Safety: Fuel quality standards also include requirements related to safety, such as flashpoint, sulfur content, and stability. Adhering to these standards helps mitigate the risk of fuel-related accidents, spills, and fires, ensuring the safe operation of diesel generators and protecting both personnel and equipment.
4. Environmental Impact: The quality of fuel used in diesel generators can impact the environment through emissions of pollutants such as particulate matter, nitrogen oxides, and sulfur dioxide. By using cleaner-burning fuel that meets environmental standards, users can reduce the ecological footprint of their diesel generators and contribute to a healthier environment.
Consequences of Using Low-Quality Fuel
Using low-quality fuel in diesel generators can have a range of negative consequences, affecting both the performance of the equipment and the overall operation of the system. Some common consequences of using low-quality fuel include:
1. Engine Damage: Low-quality fuel may contain contaminants, impurities, or water that can damage the engine components, leading to increased friction, corrosion, and wear. Over time, this can result in decreased engine efficiency, poor performance, and ultimately engine failure.
2. Reduced Efficiency: Poor-quality fuel may have inconsistent combustion properties, lower energy content, or higher levels of impurities that can reduce the efficiency of the diesel generator. This can result in higher fuel consumption, decreased power output, and increased operating costs.
3. Increased Emissions: Low-quality fuel can result in incomplete combustion, leading to higher emissions of pollutants such as carbon monoxide, hydrocarbons, and particulate matter. This not only contributes to air pollution but can also cause compliance issues with environmental regulations.
4. Maintenance Issues: Contaminated or low-quality fuel can clog fuel filters, injectors, and other components of the fuel system, leading to reduced fuel flow, poor atomization, and engine misfires. This can result in increased maintenance requirements, downtime, and higher repair costs.
Key Parameters for Evaluating Fuel Quality
When assessing the quality of fuel for use in diesel generators, several key parameters should be considered to ensure optimal performance and reliability. These parameters include:
1. Cetane Number: The cetane number is a measure of the ignition quality of diesel fuel, indicating how easily the fuel ignites and burns in the engine. Higher cetane numbers generally result in better combustion efficiency, reduced emissions, and improved cold-start performance.
2. Sulfur Content: The sulfur content of diesel fuel is an important parameter that impacts emissions of sulfur oxides (SOx) when combusted. Low-sulfur fuel is required to meet environmental regulations and reduce the environmental impact of diesel generators.
3. Water Content: Water in fuel can lead to microbial growth, fuel degradation, and corrosion in the fuel system. It is essential to maintain low water content in diesel fuel to prevent these issues and ensure the reliable operation of the generator.
4. Stability: Fuel stability refers to the ability of the fuel to resist oxidation, degradation, and formation of sediments or gums during storage. Stable fuel helps prevent fuel system clogging, injector fouling, and engine deposits, ensuring consistent performance.
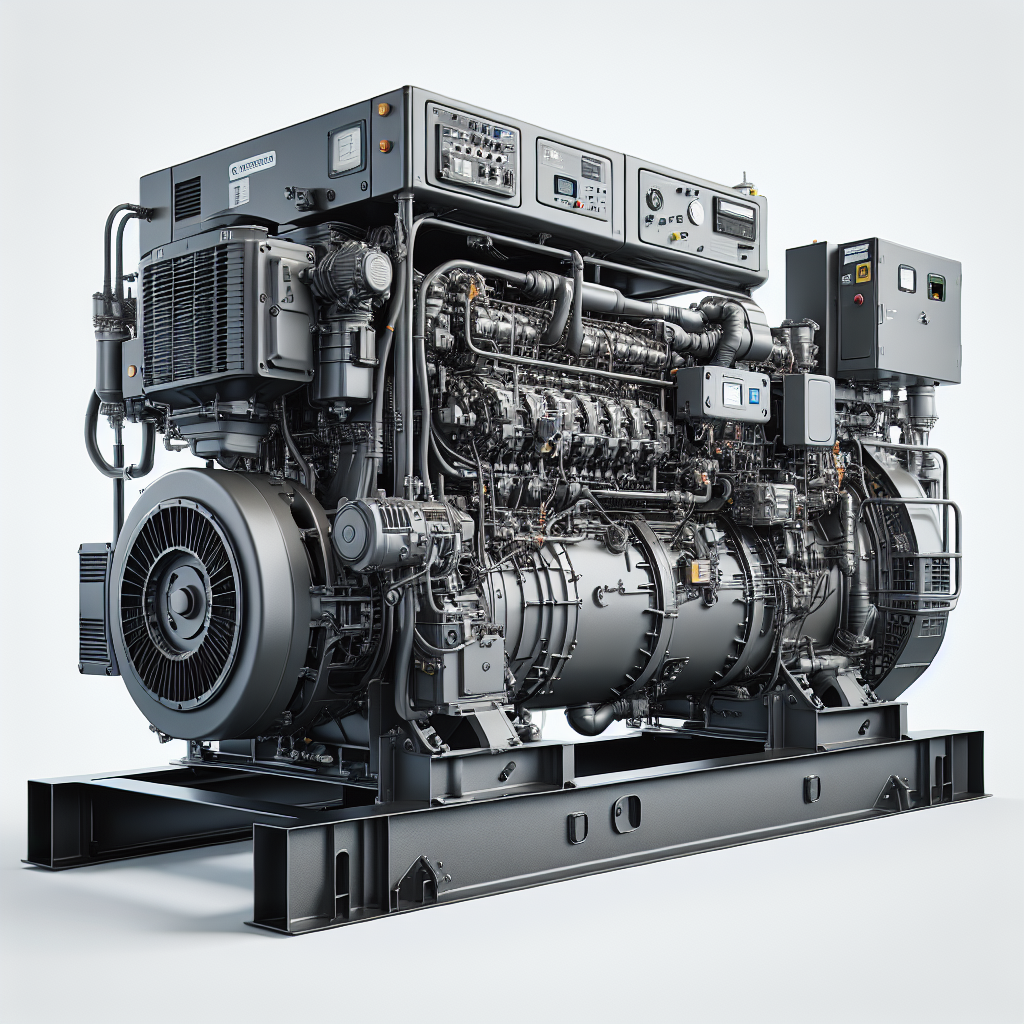
5. Lubricity: The lubricity of diesel fuel is crucial for protecting fuel system components, such as pumps and injectors, from excessive wear and damage. Low-lubricity fuel can lead to increased friction, reduced component life, and higher maintenance costs.
6. Cold-Flow Properties: Diesel fuel should have adequate cold-flow properties to prevent wax formation and gelling at low temperatures. Fuel with poor cold-flow properties can cause fuel filter plugging, fuel line blockages, and difficulties in starting the engine in cold weather.
7. Additives: Some fuel quality standards may include requirements for the use of additives, such as lubricity improvers, cetane boosters, or anti-oxidants, to enhance the performance and stability of the fuel. Adding appropriate additives can improve fuel quality and protect the engine from potential issues.
Conclusion
Ensuring the quality of fuel used in diesel generators is essential for maximizing efficiency, performance, and longevity of the equipment. By adhering to fuel quality standards and considering key parameters such as cetane number, sulfur content, water content, stability, lubricity, cold-flow properties, and additives, users can mitigate the risks associated with low-quality fuel and optimize the operation of their diesel generators.
Regular testing, monitoring, and maintenance of fuel quality are crucial steps in ensuring the reliability and safety of diesel generators. By investing in high-quality fuel that meets the required standards and specifications, users can protect their equipment, reduce operating costs, and contribute to a more sustainable and efficient power generation system.